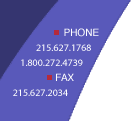 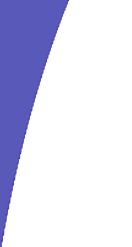 |
 |
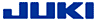
Computer-controlled, High-speed,
Lockstitch Buttonholing Machine
The machine offers increased flexibility. It achieves the
highest productivity and seam quality.
|
PDF
CATALOG
|
back
to main JUKI page
Features
The
machine eliminates oil stains on the sewing
product. |

Thanks to our
advanced dry-head technology, no lubrication
is required except for the hook section. This
eliminates oil stains on the sewing product. |
|
The machine can
be completely changed into a dry-head machine
by replacing the hook with an optional non-lubricated
hook.
(In this case, the maximum sewing speed will
be 3,300rpm.) |
|
 |
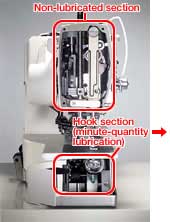 |
Only a minute-quantity
of clean oil is fed to the hook section
from the oil tank. |
|
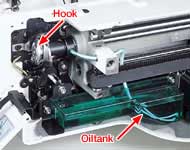 |
|
JUKI's
unique active-tension (Electronic thread-tension-control
system). |

Needle thread
tension for sewing parallel and bartacking
sections of buttonholes can be separately
controlled through the operation panel and
stored in memory according to various sewing
conditions (e.g., type of thread, type of
material and sewing speed). |
|
The machine is
able to change the needle thread tensions
at the parallel and bartacking sections of
the buttonhole, to produce a beautiful buttonhole
shape. This capability helps greatly in preventing
thread breakage. |
|
Needle thread
tension is activated at the beginning and
end of sewing. This prevents unthreading of
the needle thread, and thread fraying that
is likely to occur at the beginning of sewing. |
|
Thread tension
for basting stitching can be specified separately. |
|
 |
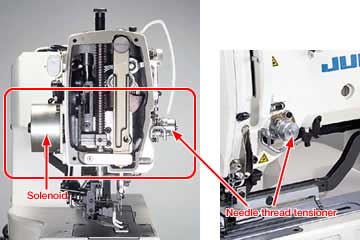 |
Frame
shape offers improved operability. |

The hollowed type
frame promises efficient sewing of vertical
buttonholes. The machine can be operated with
its head positioned horizontally. |
|
The distance from
the machine arm to the needle has been lengthened
and the left side section of the needle entry
has been reduced by a large margin. This helps
in the smooth placement of the sewing product
on the machine, thereby ensuring improved
workability. |
|
 |
The sewing product can further
be placed on the machine easily by installing
the auxiliary table (standard accessory).
In addition, the needle entry is located in
the center of the bed, promising easier positioning
of the sewing product. |
|
|
|
|
|
Basting
stitch mechanism is effective for the production
of beautiful buttonholes. |

The basting
stitch is effective on elastic materials such
as knits. Two different stitching styles are
possible, i.e., basting stitch
and joining stitch. These two
styles of stitches may also be combined. (Sewing
is carried out in the order of joining stitch,
basting stitch and regular stitch.)
Basting stitch: |
Since the needle thread
is tucked in without fail, it will never
jut out of the buttonhole seams. Basting
stitch can be sewn by nine rounds. |
Joining stitch: |
It works to prevent the
buttonhole from expanding, thereby helping
to finish beautiful buttonholes. |
|
|
 |
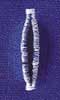 |
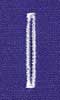 |
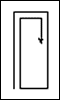 |
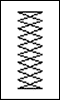 |
Without basting stitch |
With basting stitch |
Basting stitch |
Joining stitch |
(The state in which the material
is stretched in the lengthwise direction after
buttonholing) |
|
|
|
|
Sewing
settings can be easily changed. |
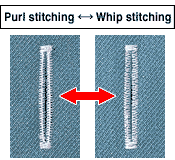 |
|
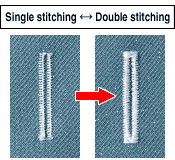 |
Purl stitching |
|
Whip stitching |
|
|
State of first-round
stitch |
|
Finished state
of double stitching |
|
(For a changeover between purl
stitch and whip stitch, threading of bobbin,
as well as the bobbin thread tension need
to be changed.) |
|
|
For double stitching,
the bartacking section is skipped and
only the parallel sections are sewn
twice. This prevents any excessively
tight finishes in the bartacking section
of the buttonhole. |
|
First- and second-round
stitches can be sewn using different
stitch widths. |
|
|
|
|
|
|
Shorter
length of bobbin thread remaining on the material. |

The new model
of the bobbin thread trimming mechanism cuts
the bobbin thread so that it leaves a shorter
length of thread on the material.
Furthermore, the machine produces bartacks
at the end of sewing, thereby preventing finished
seams from coming undone. |
|
With the soft-start
function, the number of stitches, as well
as the sewing speed at the start of sewing
can be specified, thereby preventing the needle
thread from slipping off from the needle eyelet.
(From the first to the fifth stitches, the
sewing speed can be specified on a stitch-by-stitch
basis.) |
|
|
|
|
The
machine is equipped with a multiple knife-dropping
function. |

Thanks to the
multiple knife-dropping function, it is no
longer required that the knife be changed
at the time the buttonhole size is changed.
The number of knife dropping times can be
automatically set according to the buttonholing
size in cases where the buttonhole size is
frequently changed for small-lot productions
or during the cycle sewing of buttonholes
that are different in size. |
|
The double-acting
solenoid type knife mechanism is free from
the faulty dropping/returning of the knife.
In addition, the knife pressure can be changed
according to the material to be sewn. |
|
The knife supports
sewing lengths of 41mm at the maximum. In
addition, knife mechanisms for 70mm and 120mm
are optionally available. With this, slots
such as the belt holes of child seat belts
can be buttonholed. |
|
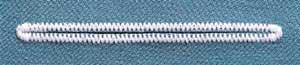
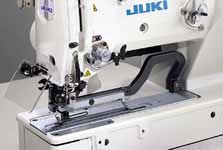 |
|
|
Cycle
sewing and continuous sewing. |

Twenty different programs can
be registered, and as many as 15 different
patterns can be stored in one program. |
The machine is able to continuously
sew two or more different patterns without
requiring the work clamp foot to be lifted.
As may as 20 programs can be registered, and
six different patterns can be stored in one
program.
(Related parts need to be exchanged for optional
ones.) |

The needle bar
can be shifted to the rightmost end position
with the work clamp foot lowered.
This facilitates threading of the machine
head. |
|
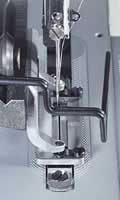 |
 |
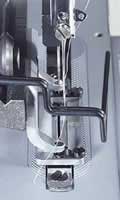 |
Position of the needle
bar during sewing |
|
The needle bar can be
shifted to the right at the time of
threading |
|
|
 |
Many
functions of the pedal. |

The machine is
provided as standard with a newly-developed
auto-lifter driven by a stepping motor. This
helps reduce the operator's fatigue. This
helps reduce operator fatigue. As for the
pedal, one-pedal and two-pedal models can
both be changed over and the intermediate
stop, which facilitates positioning of the
sewing product, can be specified. |
|
 |
The work clamp
foot lift can be set as desired.
The reverse-rotation needle-up function offers
a maximum work clamp foot lift of 17mm. |
|
Explanation
of pedal motion |
Pedal
motion |
Pedal
type |
2-pedal |
1-pedal
(without intermediate position) |
1-pedal
(with intermediate position) |
Initial position |
Intermediate
position |
Maximum
position |
Maximum
position |
Setting
of sewing product |
Presser goes
up as high as the pedal toe down amount of
the left side pedal.
Presser comes down when the left side pedal
is depressed.
 Sewing
position |
The first
step of the right side pedal
 Sewing
position |
The first
step of the right side pedal
 Intermediate
position

The second step of the right side pedal
 Sewing
position |
Start of
sewing |
The right
side pedal is depressed. |
The second
step of the right side pedal |
The third
step of the right side pedal |
End of sewing |
Presser
automatically goes up to intermediate position. |
Presser
automatically goes up to maximum position. |
Presser
automatically goes up to maximum position. |
|
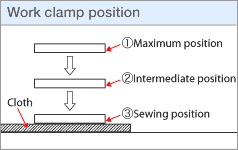 |
|
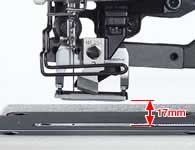 |
Major
drive mechanism is electronically controlled. |

An electronic
control feature has been adopted for the material
feed mechanism, needle rocking mechanism,
needle thread trimming mechanism, bobbin thread
trimming mechanism, cloth cutting knife mechanism
and presser bar lifting mechanism. In addition,
mechanisms such as V-belts, stop-motion mechanisms
and cams have been substantially reduced to
ensure operation with lower vibration and
noise. |
|
A direct-driven
system that directly connects the compact
AC servomotor to the main shaft has been adopted. |
|
All adjustment
values are entered as data. They can be set
or stored in the memory on the operation panel. |
|
|
 |
|
|
Specifications
Sewing
speed |
Max.:
4,200rpm, Normal: 3,600rpm |
When the
non-lubricated hook (optional) is used: 3,300rpm |
Needle bar stroke |
34.6mm |
Size of cloth cutting
knife |
6.4~31.8mm
(1/4"~1-1/4") |
Bartacking width |
Max. 5.0mm
(with special-specification part: Max. 10mm*) |
Buttonhole length |
Max. 41mm
(optional: 70mm, 120mm) |
Precision of needle throwing
mechanism |
0.05mm |
Thread tension |
Active-tension
(electronic thread-tension-control system) |
Number of stitches |
Automatically
computed from the size of the buttonhole and stitch pitch |
Needle (at the time of
delivery) |
DP x 5
(#11J) #11J~#14J |
Hook |
DP type,
full-rotary hook |
Non-lubricated
hook (optional) |
Lift of the work clamp |
14mm (17mm
when the reverse-rotation needle-up function is used) |
Auto-lifter |
Provided
as standard (stepping motor type) |
Needle throwing drive
system |
Driven
by a stepping motor |
Cloth feeding knife drive
system |
Intermittent
feed by a stepping motor |
Cloth cutting knife drive
system |
By a double-acting
solenoid |
Standard patterns |
30 patterns |
Number of patterns that
can be input |
Max. 99
patterns |
Bobbin thread winder |
Built-in
the machine head |
Machine head drive system |
Compact
AC servomotor (direct-drive system) |
Power requirement/ Power
consumption |
Single-phase
220V, 230V, 240V 3-phase 200~240V/650VA |
Lubrication |
Only the
hook section needs a minute-quantity lubrication.
* No lubrication is required when the non-lubricated hook
(optional) is used. |
Lubricating oil |
Hook:
JUKI New Defrix Oil NO.1 (equivalent to ISO VG7) |
Total weight |
112kg |
Adobe
Acrobat Reader is required to
view .pdf files.
|
|
|